Carnival Glass
What is Carnival glass?
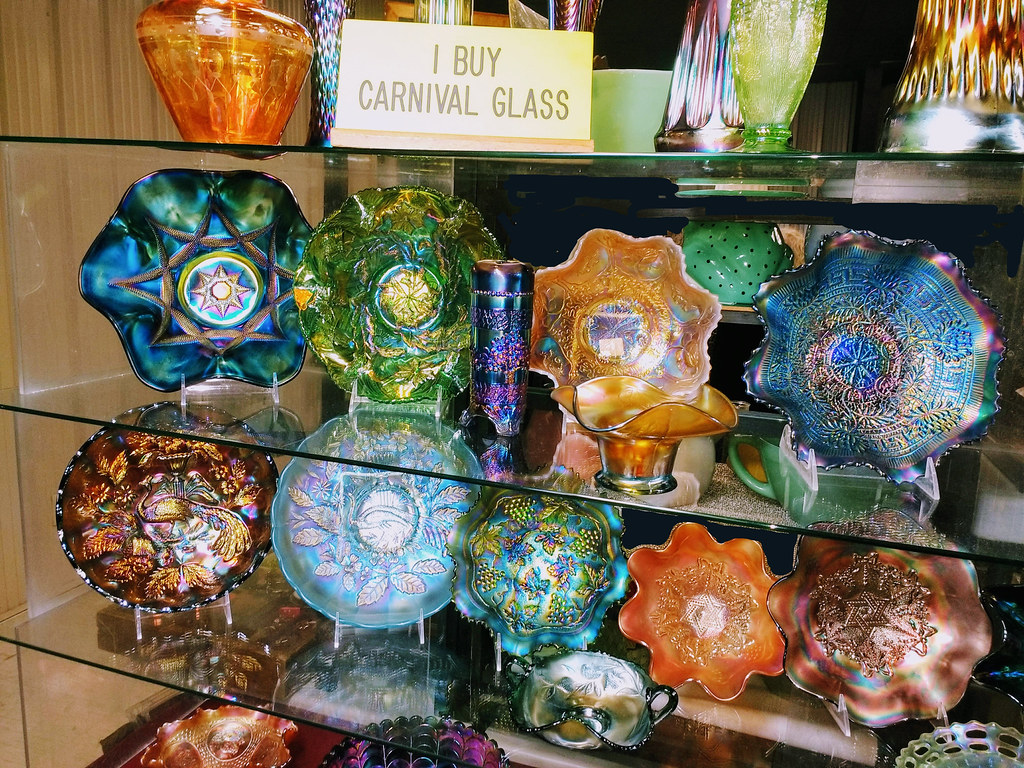
Carnival glass is a type of pressed or molded glass manufactured during the early 1900s. Vastly cheaper than art glass to produce yet equally as alluring, Carnival glass quickly became a staple item in many American households. It was renowned for both its aesthetic qualities as decor and functionality as dishware. Alongside its striking iridescence, the base glass was also produced in a variety of colors, such as the popular marigold, blue (cobalt), amethyst, green, or opalescent hues. Manufacturers often produced their pieces in a variety of shapes that included a wide range of design motifs, each selected based on consumer demand and depending on the personal styles of each company.
Fenton, for example, often shaped their glassware with a ruffled edge, while Northwood applied more of a “pie crust” edge. Fenton’s Carnival glassware line debuted in 1907, known then as Iridie or Iridil glass. Fenton’s products were an instant success, quickly spawning several subsequent copycats and eventually becoming a globalized sensation. Previously, “Pompeiian Iridescent,” “Venitian Art,” “Dope glass,” “Baking Powder glass,” “Taffeta glass,” and “Mexican Aurora” had also been used to describe the kaleidoscopic glassware before designers elected “Carnival glass” as a semi-official title. Though their fantastical colors surely lent a carnivalesque sense of wonder and amazement to the pieces, the name actually comes from how surplus pieces were offered as prizes at local carnivals or fairs once such designs fell out of fashion during the 1930s.
Significance
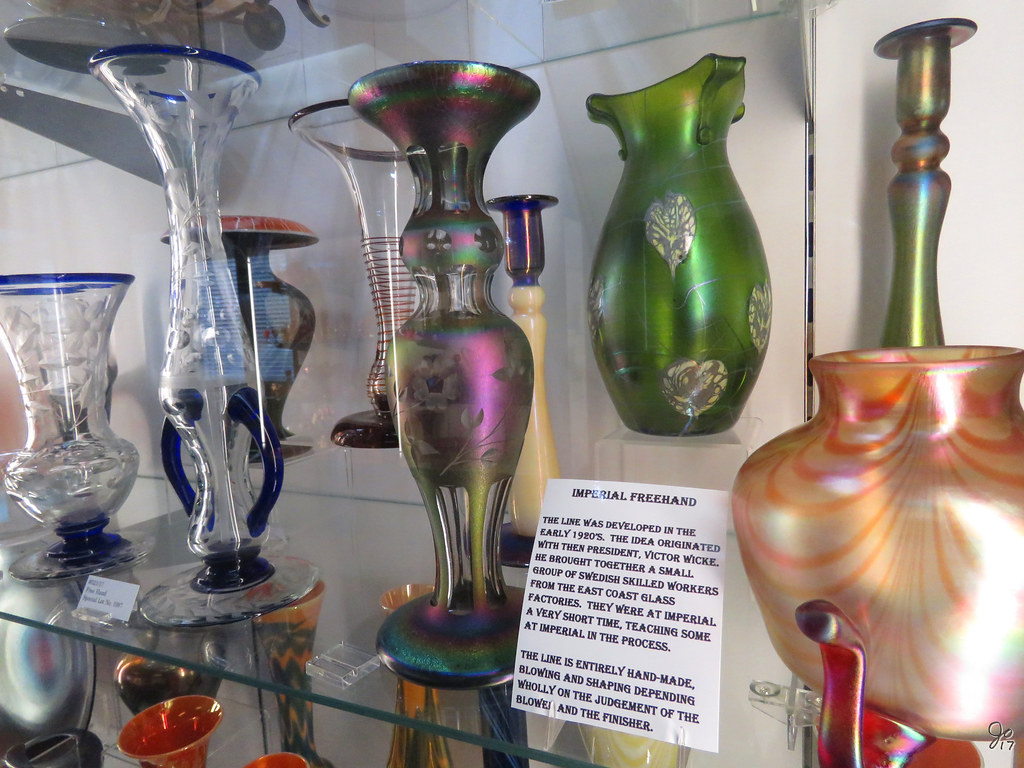
Throughout the twentieth century, the glassware industry transformed the very nature of American consumerism. While Tiffany’s glass had become a signifier of wealth and privilege—despite his somewhat ill-construed desire for an egalitarian notion of beauty—mass-produced factory glassware pieces were the most accessible form of decorative luxury for those of lower economic classes.
The industry began with the invention of pressed glass in the early 1800s, the most advanced and profitable technique for glassmaking at the time. Glass presses made it possible to easily manufacture and reproduce plain or patterned glassware without the use of highly skilled, yet costly glassblowers. Cutting these costs made pieces more affordable to the average consumer, and redirected focus on devising new and imaginative ways to manufacture glassware. The following are various glass types invented during this period:
- Sulfide relief portraits
- Italian millefiori—meaning ‘a thousand flowers’
- Novelties
- Silvered glass
- Engraved glass
- Cameo glass
- Color effects such as Amberina, Peachblow, or Burmese glass
- Pomona etched glass
- French pâte de verre
- Uranium or Vaseline glass
and, last, but certainly not least, Carnival glass.
Between 1905 and 1930, several design companies across the world manufactured glass with an iridized quality. The most notable producers in the United States include the Fenton Art Glass Co., the Imperial Glass Co., Dugan-Diamond, Northwood Glass Co., and the Millersburg Glass Co., all founded in the tri-state area of the United States: Ohio, Pennsylvania, and West Virginia.
Due to its status as a cheaply produced material, Carnival glass came to be known as “Poor Man’s Tiffany,” as many likened it to the iridized Favrile glass popularized in prior decades by Louis Comfort Tiffany, the acclaimed glassware designer. While Tiffany’s art glass was created by altering the chemical composition of the glass itself, the characteristic, iridescent luster of Carnival glass was achieved by spraying a chemical solution consisting of metallic salts on the surface of the glass before it was fired. Then, the glass would be properly shaped, creating another type of glass known as Stretch glass, of which the surface will often resemble onionskin.
For reference, the following video demonstrates the process of iridizing glass:
The general public favored glassware that was both beautiful and functional, so as not to be a waste of hard-earned financial resources. Many people relied on companies to produce quality dishware, most often in the forms of breakfast, table, water, and dressing table sets; bowls for candy or nuts; flower vases; punch bowls and cups for parties and other events; and even small novelty items, such as candlesticks, toothpick holders, and miniature dishes modeled after swans. Even if the differences between Tiffany glass and the so-called “Poor Man’s Tiffany” were quite stark, the demand for simultaneously practical and decorative glassware far outweighed any concerns over how similar the products were. Mass-produced factory glass was en vogue, so to speak.
Later, Carnival glass experienced a resurgence of popularity in the 1960s, with the Imperial Glass Company reissuing several decommissioned patterns. And, nearly four decades later, many members of the glassware-collecting community have observed recent spikes in the interest in Carnival glass, as both veterans and newcomers to the collecting world set their sights on the glamorous, yet modestly-priced antiques.